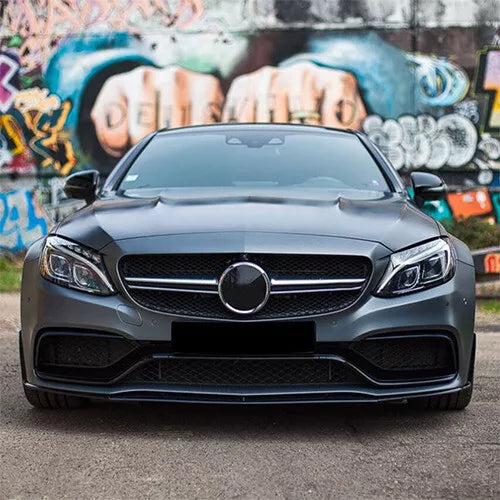
Will Your Running Boards Last? The Finish Makes All the Difference
The finish on your vehicle's running boards isn't just about looks—it plays a crucial role in how long these accessories will last in tough conditions. When you invest in quality running boards, knowing how different finishes affect long term durability can save you from having to replace them early or do extra maintenance.
How Running Board Finishes Impact Overall Lifespan
The protective coating on truck running boards is your first defense against environmental threats. High quality finishes create a barrier that protects the material underneath from moisture, road salt, sun damage, and impacts. Without good protection, even the strongest aluminum running boards or steel side steps will eventually break down.
Powder coating has become one of the most durable finishes for running boards on the market. This process uses electricity to apply dry powder to the metal surface before heating it to cure. The result is a thick, even coating that guards against chips, scratches, and rust. These boards usually last several years longer than those with regular paint, especially in places with harsh weather.
Anodized aluminum is another top finish option that greatly boosts durability. This chemical process increases the thickness of the natural oxide layer on the aluminum surface, creating a rust resistant finish that becomes part of the base material rather than just sitting on top. This makes it almost impossible for the protective layer to chip or peel off, ensuring long lasting performance even when often exposed to harsh elements.
Material Specific Finish Considerations
The base material of your running boards greatly influences which finish will provide the best durability. Steel running boards usually benefit most from heavy duty coating or special paint processes that include several protective layers. Without these complete treatments, steel remains very vulnerable to rust, which can quickly weaken its structure.
For aluminum running boards, both anodizing and powder coating offer excellent durability, though they protect in different ways. Anodized finishes enhance aluminum's natural rust resistance while providing a hardened surface that resists scratches. Meanwhile, powder coating offers better protection against chemicals and may keep its color better over many years in the sun.
Composite running boards usually include UV blockers and special sealants during manufacturing. These built in protective elements make composite materials naturally weather resistant, though adding clear coat finishes can further extend their life by preventing color fading and surface damage.
Environmental Factors and Finish Performance
The climate where you drive plays a big role in determining which running board finish will give the best durability. In coastal areas with high salt in the air, anodized aluminum or marine grade coatings provide superior protection against the faster rust that salt causes. These special finishes create a seal that prevents salt particles from starting the rusting process on metal surfaces.
For vehicles in regions with harsh winters and frequent road salt, protective finishes with several layers work best. The combination of primers, main coats, and clear sealants ensures that even if the outer layer gets damaged by road debris or salt, inner protective layers still guard the base material from rust.
Desert environments create unique challenges due to intense sun and extreme temperatures. In these conditions, finishes with built-in UV protection prevent color fading and surface damage that can lead to cracking and material failure. Many top running boards now feature special UV resistant clear coats made specifically for vehicles in sunny regions.
Maintenance Requirements Based on Finish Type
Different running board finishes need varying levels of care to maintain good durability. Chrome-plated running boards, while very shiny and attractive, need regular cleaning and polishing to prevent pitting and rust, especially when exposed to road salt or coastal air. The upkeep can be substantial, making chrome less practical for those wanting maximum durability with minimal maintenance.
Textured finishes from powder coating sit at the opposite end of the maintenance spectrum. These finishes not only provide excellent protection but also hide minor scratches and dirt, needing only occasional cleaning to maintain their protective abilities. For busy vehicle owners who care more about durability than showroom looks, textured finishes offer an ideal balance.
Clear-coated aluminum running boards deliver impressive durability when properly maintained. Regular cleaning to remove road grime and occasional use of aluminum protectant can extend the life of these finishes by many years. The key maintenance requirement involves quickly fixing any clear coat damage to prevent moisture from reaching the aluminum underneath.
Impact Resistance Across Different Finishes
The ability to withstand impacts without losing protection is a critical aspect of running board durability. Elastic finishes, which contain rubber like compounds, provide better resistance to stone chips and minor impacts compared to rigid coating systems. These special finishes can absorb and spread impact forces, preventing them from transferring to the base material where they might cause dents or structural damage.
Regular paint finishes, even when professionally applied, typically offer the least impact resistance among common running board finishes. Their relatively thin application provides minimal cushioning against flying debris, making them prone to chips and scratches that can quickly become starting points for rust in harsh environments.
Protection systems with two layers combine the benefits of different finish types to maximize impact resistance. For instance, some premium running boards feature a tough elastic base coat for impact absorption covered by a clear ceramic coating that provides superior scratch resistance. This combination delivers exceptional durability in high-debris environments like construction sites or unpaved country roads.
Weathering and Aging Characteristics
How a running board's finish weathers over time directly impacts its long-term durability. Finishes with UV protection maintain their protective properties much longer than standard alternatives when regularly exposed to sunlight. Without these special additives, many finishes will gradually break down under UV exposure, leading to cracking, chalking, or peeling that compromises their protective abilities.
Finishes cured with heat like professional powder coating show superior aging compared to air dried alternatives. The molecular bonding that happens during the heat curing process creates a more stable finish that resists the tiny expansion and contraction cycles caused by temperature changes. This stability means fewer cracks develop over time and ultimately extends the running board's useful life.
The edge protection provided by different finishes also influences long term durability. Electric application methods, including powder coating, pull the finish material around edges and into recessed areas, ensuring complete coverage. This thorough protection prevents edge rust—a common failure point for running boards with regular finishes that often have thinner coverage along edges and corners.
Finish Quality and Installation Considerations
Even the most advanced finish technology provides limited durability benefits if poorly applied. Professional finish application ensures proper surface preparation, including thorough cleaning, degreasing, and often blasting to create an optimal sticking surface. This careful preparation prevents early finish failure that often occurs with poorly prepared surfaces.
Finishes applied at the factory typically offer superior durability compared to aftermarket options due to controlled application environments and industrial-grade curing processes. Manufacturers can maintain precise temperature, humidity, and dust control while applying finishes, resulting in more consistent protection across the entire running board surface.
For those considering aftermarket finish options to enhance durability, professional application remains critical. Experienced applicators understand the importance of proper pretreatment processes, including phosphate treatments for steel or chromate treatments for aluminum, which greatly improve finish adhesion and rust resistance.
Comparing Durability of Premium vs. Budget Finishes
The durability gap between premium and budget running board finishes goes far beyond initial appearance. Top quality finishes often include rust inhibitors that actively suppress oxidation reactions even if moisture gets through the protective layer. This active protection mechanism provides a significant durability advantage over basic finishes that rely solely on creating a physical barrier.
Finish systems with several stages are found in most premium running board options, with distinct layers performing specific protective functions. For example, a zinc rich primer provides sacrificial protection, while later layers deliver barrier protection before a final topcoat adds UV and chemical resistance. This thorough approach dramatically outperforms single layer budget finishes in long term durability testing.
The thickness consistency of applied finishes also varies dramatically between premium and budget options. Even application control ensures that every surface area receives adequate protection without excessive buildup that might lead to sticking issues. Budget finishes often show significant thickness variations, creating vulnerable thin spots that can become early failure points when exposed to harsh conditions.
Conclusion
The finish quality on your running boards is a critical factor in determining their overall durability and lifespan. Far from being merely for looks, these protective systems shield the underlying materials from rust, impacts, and environmental damage that would otherwise quickly compromise function. By selecting running boards with appropriate high-quality finishes matched to your specific driving conditions and maintenance preferences, you can significantly extend their service life while maintaining their appearance and performance capabilities.
FAQs
What running board finish offers the best salt rust resistance?
Anodized aluminum running boards typically provide superior salt rust resistance, as the chemical process creates an integrated oxide layer that prevents salt penetration, unlike applied coatings that can chip or scratch.
How often should running boards with powder coating be cleaned to ensure maximum durability?
These running boards should be cleaned monthly in normal conditions and weekly in harsh environments (coastal areas or winter road salt exposure), with yearly inspection for damage and touch-up of any damaged areas to maintain optimal durability.
Can factory finishes on running boards be made better for extreme conditions?
Yes, factory finishes can be enhanced with aftermarket ceramic coatings or industrial-grade clear protectants that provide an extra protective layer against extreme conditions, though proper application by professionals is essential for effectiveness.